Manufacturing Case Study
Client Profile
Solutions
- Centerline
- Training & Development
- Root Cause Analysis
- CIL (Clean, Inspect, Lubrication)
- Shop Floor Situational Coaching
- Visual Management
- Speed Accumulation Lost Time (SALT)
Challenge
- Operators not experienced and have very little interaction with their assets
- Site/Lines suffer from a high level of downtime/short stops
- Each shift has their preferred machine settings and way to “run”
- Past experience leads to unnecessary tinkering
- Changeovers are completed with little documentation
- Attempting to identify out-of-set-point settings leads to lengthy troubleshooting
- There is no way to return the machine to “baseline” because the “baseline” isn’t documented
- Material vendors blame material issues on poorly maintained equipment
- Operators rely heavily on Maintenance for equipment setup and adjustment
Approach
- Deep-cleaned the top sources of loss, using heat maps to identify critical focus areas
- CIL standards built to maintain deep clean
- Conducted operator & technical baselines
- Prioritized work orders
Centerline – Find the settings
- Developed a master list of adjustment points
- Facilitated a red dot exercise to eliminate points that should not be adjusted
- Identified changeover and run-right settings for critical adjustment points
- Validated settings across multiple changeovers and runs of each size
Sustain – Maintain the system
- Visual boards installed with CIL checklists and run-right setting audit sheets
- Change control process coached
Results
- Provided operational stability by eliminating variation due to “tinkering” with any process
- All operators trained on one right way – everyone runs the process at best performance settings
- Provides a “home base” for changeovers and for troubleshooting issues during production runs
- Raw material issues identified and escalated through consistent machine setting
- Improved effectiveness of operator training and allowed for additional changeover and troubleshooting tasks to be shifted from maintenance to operations
- Line utilization improved by 19% over baseline
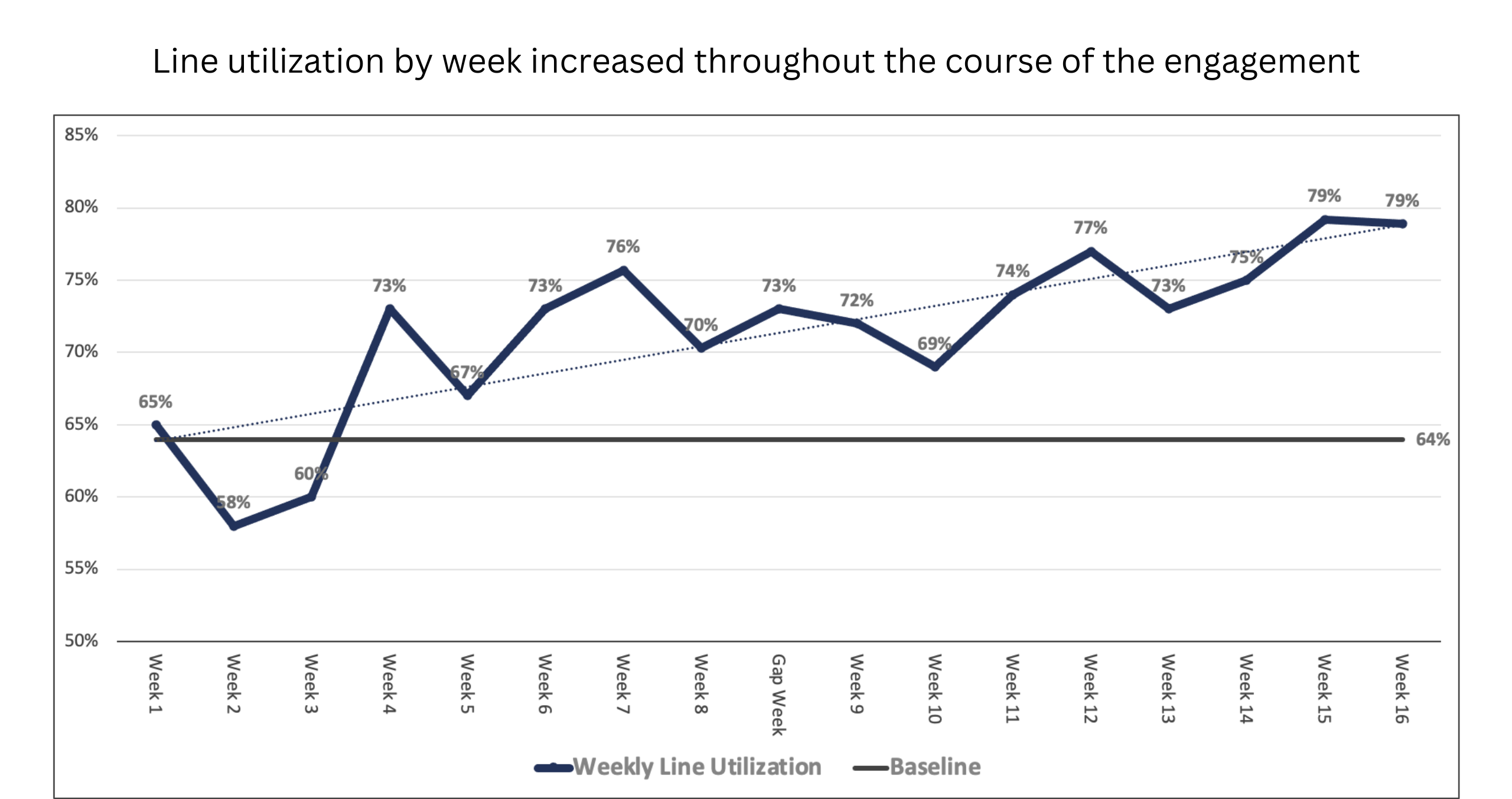